Signalanalyse mit prozessgenerierten Wavelets für die Zustandsüberwachung von Profilschienenführungen
Working Group: | WG Industrial Mathematics |
Leadership: | Prof. Dr. Dr. h.c. Peter Maaß ((0421) 218-63801, E-Mail: pmaass@math.uni-bremen.de ) |
Processor: | Dr. Ludger Prünte |
Funding: | Zentrale Forschungsförderung Uni Bremen |
Project partner: | Prof. Dr. Bernd Kuhfuß, WZM |
Time period: | 01.10.2004 - 30.09.2007 |
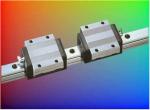
Situation
The aim of the project is the development of a numerical analytical method which expands the well-known Discrete-Wavelet-Transformation (DWT) not by using standard wavelets but by deriving a basic wavelet directly from the process. The required coefficients for detail and approximation filters are designed from this basic wavelet. This procedure combines the benefits of wave band decomposition of the Discrete-Wavelet-Transformation with the characteristics of pattern detection by scaled cross-correlation of the Continuous-Wavelet-Transformation (CWT). These aspects can only be used reasonably for the interpretation of coefficient levels if it succeeds to derive patterns from the process (signal extracts) and to transform it to discrete wavelet filters. The method shall be developed by using patterns of equipment condition monitoring of linear guideways. This important element of machine tools is chosen because it is sufficiently complex from the influencing variables to judge the ability of the numerical process. Finally it should be possible to use machine immanent resp. accessable signals, e.g., electric drives for condition monitoring without additional sensors. As these signals only reproduce the process very indirectly a condition monitoring, e.g. abrasion of roller elements, can only be effective if it is very sensitive and stable as well.
Identification of characteristic process patterns of the Continuous-Wavelet-Transformation (CWT). The condition monitoring of linear guideways is characterized by providing localized characteristics of the normal working condition and of the monitored abrasion condition. Compared to rotarory ball bearings the monitoring of linear guideways shows a transient characteristic. This is due to the production and assembly accurracy of guide systems. Varying preloads across the traverse path will already influence the normal working condition. A machine tool does not consistantly make use of the whole traverse path of the axis so the abrasion of slideways as disturbing condition is locally limited. The transient characteristics patterns must be sensitively found by CWT out of measurable signals and must be segregated.
Aggregation of coefficient levels to variables. The transformed measurement signals are available as coefficient levels. The information contained must be aggregated to quantative and informative signals in order to obtain the aim basics of condition monitoring. For that purpose methods shall be developed to describe the characteristic features of process generated (so called selflet) coefficients with informative characteristics.
Design of filter coefficients for the Discrete-Wavelet-Transformation (DWT). The Continuous-Wavelet-Transformation is not adapted for the online equipment condition monitoring of technical complex processes. The used fast transformation is performed of the DWT in principle, but up to now the design of qualified filters based on process-generated basic wavelets is missing.