Minimal Identification and Modelling of the Dynamics of Industrial Robots
Working Group: | WG Optimization and Optimal Control |
Leadership: | Prof. Dr. Christof Büskens ((0421) 218-63861, E-Mail: bueskens@math.uni-bremen.de ) |
Processor: | Peter Lasch |
Project partner: |
SEF Roboter GmbH, Scharnebeck ADC GmbH, Scharnebeck |
Time period: | 01.05.2004 - 30.04.2005 |
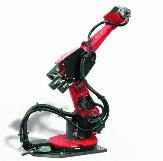
Even though exact CAD models of new robots are produced during the design phase, said models being able to be used to ascertain the characteristics of the dynamic model, in practice industrial robots often exhibit a dynamic behaviour which deviates from this. Even robots of identical construction can demonstrate different system parameters.
The scope of the cooperation project will therefore include the development of a method to quickly and reliably identify robot model parameters. In order to continue to meet the real-time requirements when designing the path, the model will, at the same time, be reduced to the minimum complexity which is necessary. The dynamic behaviour will thus be modelled only in the relevant areas and parameters will be deleted if not taking them into consideration would not cause a behaviour which is different to the actual behaviour. To achieve the desired control accuracy, measurement data is recorded every 5ms. This leads to the order of 5000 records for a typical motion sequence, which are processed further. At present, with less than 10% of this data one requires a computer time of around 1h. One frequently obtains local minima which do not fulfil the optimisation objective, however, so that the computation has to be repeated.