HVDC-MMC_with_MPC: A new method for reducing the power dissipation of MMC high-voltage converters using MPC
Working Group: | WG Optimization and Optimal Control |
Leadership: | Prof. Dr. Christof Büskens ((0421) 218-63861, E-Mail: bueskens@math.uni-bremen.de ) |
Processor: | Dr. Chathura Wanigasekara |
Funding: | Bundesministerium für Wirtschaft und Energie (BMWi) |
Project partner: |
Institut für Automatisierungstechnik (IAT), Universität Bremen Siemens AG |
Time period: | 01.07.2020 - 30.06.2023 |
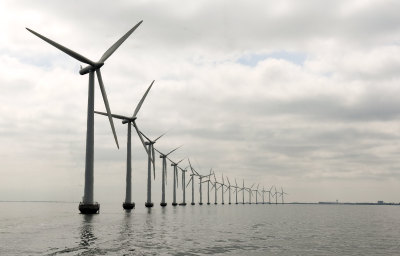
The research project focuses on the development, implementation and testing of a powerful and real-time capable non-linear model predictive control (NMPC) for the control of a modular high voltage inverter (HVDC-MMC). An NMPC controller has internally a simplified complete model of the process dynamics, which is used to predict the future course of the process variables over a limited period of time. For a given cost functional, a numerical optimization procedure can be used to determine the optimal mode of operation over the considered future time horizon. However, only the first step is transferred to the process. In the next sampling step, the considered time period is shifted and the entire calculation is performed again. By this procedure new measured values are included in each time step and thus not measured disturbances and deviations between process model and real process behaviour are considered.
Since the solution of the optimization problem requires calculation time in each step, dealing with limitations of calculation time and capacity is a challenge when implementing MPC methods in highly dynamic real-time applications. For this purpose, a completely new approach, tailored to the characteristic technological properties of converters, is to be pursued. This approach will make it possible to overcome the computation time problem despite the necessary high-frequency switching operations and to use the advantages of MPC processes for minimizing losses in extra-high voltage converters.
Translated with www.DeepL.com/Translator (free version)
Image: „Middelgruden Offshore Wind Farm in Denmark“ by United Nations Photo, licenced under CC BY-NC-ND 2.0 (https://creativecommons.org/licenses/by-nc-nd/2.0/)