Optimisation of Thermo-Mechanical Processes with Laser Welding
Working Group: | WG Optimization and Optimal Control |
Leadership: | Prof. Dr. Christof Büskens ((0421) 218-63861, E-Mail: bueskens@math.uni-bremen.de ) |
Processor: | |
Funding: | Bayrisches Staatsministerium |
Project partner: |
Prof. Dr. Ulrich Rüde, Lehrstuhl für Systemsimulation, Universität Erlangen Neue Materialien Bayreuth GmbH Prof. Dr. Hans-Josef Pesch, Universität Bayreuth Verena Petzet, Universität Bayreuth |
Time period: | 01.01.2003 - 31.03.2004 |
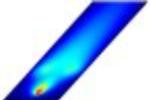
The customary way of avoiding hot cracks, selecting suitable weld parameters or developing filler materials which are not susceptible to cracks, are largely based on trial-and-error experiments. They are time-consuming and expensive. Numerical simulation and optimisation can provide intelligent solutions here, as well. As part of the project, two methods were virtually tested by simulation for their potential to minimise hot crack formation:
- The multiple beam process: this process involves the generation of compressive stresses by introducing heat locally using additional laser beams, said compressive stresses opposing the tensile stresses which arise during laser welding. By optimising the position, active area and intensity of the additional beams the hot crack formation will be minimised.
- Optimisation of the material composition: optimisation techniques will be used to select suitable filler metals, which have an effect on the metallurgical properties, so that the hot crack formation is minimised.
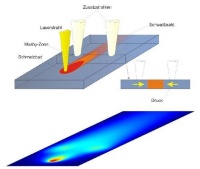
and intensity of auxiliary beams determined by numerical simulation of multi-beam welding.
Parallel FEM (finite element method) software developed by Neue Materialien Bayreuth GmbH has been tested on a Linux cluster and has shown that to solve the optimisation problem with the number of parameters which occur in industrial applications it is essential to use super computers, e.g. from large clusters. This makes it possible to realise the parallelisation on various scales (coarse, medium, and fine granular). The mathematical model of laser welding and hence the basis for the numerical simulation and optimisation is a coupled system of partial differential algebraic equations to describe the heat conduction and the thermo-mechanical stresses, and an ordinary system of differential equations to describe the metallurgical processes of the phase transition.