Optimal Production Engineering in Microsystem Technology
Working Group: | Former WG Numerics |
Leadership: | Prof. Dr. Angelika Bunse-Gerstner (E-Mail: bunse-gerstner@math.uni-bremen.de ) |
Processor: | |
Project partner: | microFAB Bremen GmbH |
Time period: | since |
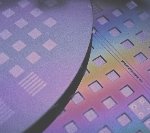
If large companies have to manufacture large numbers of pieces, they can design their production lines so that bottlenecks in the production flow can be prevented from the outset. Several machining stations are available here for time-consuming processes. Moreover, maintenance work and machine outages caused by redundancy in the system capacities do not affect the production.
When manufacturing smaller numbers of pieces for special components as ordered by small and medium-sized companies, it is often not worth buying more machines and it is preferable if existing equipment can be used to maximum efficiency.
The sequence in which the wafers have to pass through the individual stations is fixed. One workpiece can be machined repeatedly at individual stations, however. For the different stations there now has to be a plan as to which wafers will undergo subsequent processing next so that the productivity of the system is optimised and bottlenecks are avoided.
This combinatorial optimisation problem is heavily dependent on the critical path. The size of the problem - several wafers are each machined simultaneously in around 200 stages at 20 stations - means that very high computing times must be expected. The parallelisation of this combinatorial problem, to shorten the computer time, is easily possible using the solution strategies planned, however.