Online Optimisation of Cogeneration Plants
Working Group: | WG Optimization and Optimal Control |
Leadership: | Prof. Dr. Christof Büskens ((0421) 218-63861, E-Mail: bueskens@math.uni-bremen.de ) |
Processor: | Peter Lasch |
Funding: | Enable Energy Solutions GmbH |
Project partner: | Enable Energy Solutions GmbH, Bad Rothenfelde |
Time period: | since 01.06.2004 |
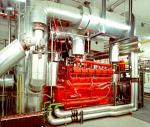
Cogeneration plants are distinguished, in particular, by their high efficiency. Whereas generating electricity in power plants converts only 30-40% of the energy contained in the fuel into electricity, cogeneration plants can convert up to 90% of the primary energy used into electricity and heat.
The complete field of industrial cogeneration plants has fundamentally changed over recent years, however, and has become very complex. Restrictions such as the KWK-Gesetz (Law on Cogeneration Plants), the KWKMod.-Gesetz (Law on Upgrading Cogeneration Plants), the green tax, higher prices for natural gas, the liberalisation of the market for the supply of electricity and CO2 emission trading, ensure that these plants can only be operated with a lot of previous knowledge and a corresponding higher staffing requirement. This has meant that many cogeneration plants have become incalculable cost factors for the companies. Various studies indicate, however, that the greatest potentials for cogeneration and the associated politico-economic favourable CO2 reduction potentials are to be found in the industrial sector.
This project will incorporate all technical possibilities and the diverse economic peripheral conditions of the location to achieve optimal online operation of the cogeneration plant. To this end, the behaviour of various standard components found in power stations will be thermodynamically computed. The theoretical results will be compared with data based on previous results (e.g. corresponding outside temperatures, pollution level, GT compressors etc.) before being subsequently processed in the dynamics of the entire power plant. Since the peripheral conditions are permanently changing, the optimal way of operation will be determined in a predictive way, to a certain extent, for a given prediction horizon. The computed results provide both the operator and the controller with transparency and make the use of industrial cogeneration plants calculable again.
From a mathematical point of view, this is a non-linear optimisation problem with equation and inequation constraints, since the output of the power plant is given as a function of the input date for the prediction horizon.
Records from three years, all measured at fifteen minute intervals, are available. These have to be integrated into a model. Until now, this adaption has only been performed using data for one month so that seasonal variations could not be included by the model.
An application has been made to continue and expand the project to consider environmental aspects, in particular, such as the reduction of CO2, waste heat, soot and slag, conservation of fossil fuels and relieving the pressure on large-scale power plants which create more environmental pollution. Furthermore, it is possible to determine the environmental pollution in advance.
Part of this project will be to represent the various power plant components of the cogeneration system of a coffee processing company in Bremen by mathematical-numerical simulation modules and to compute them thermodynamically. The theoretical results of the modules will be compared with historical data from a database (e.g. outside temperature, level of pollution etc) before being linked into the overall power plant simulation. The problem here also is how to integrate the available data into a mathematical model.
A further advantage of the method consists in the fact that the results obtained in the course of the project do not require that an existing plant be altered. The methodology will be applicable to existing and new plants.