Model predictive control of the live steam quantity in power plants
Working Group: | WG Optimization and Optimal Control |
Leadership: |
Prof. Dr. Christof Büskens ((0421) 218-63861, E-Mail: bueskens@math.uni-bremen.de )
Dr. Matthias Knauer ((0421) 218-63863, E-Mail: knauer@math.uni-bremen.de) |
Processor: | Dr.-Ing. Friedrich Kohlmai |
Funding: | Bundesministerium für Wirtschaft und Energie (BMWi) |
Project partner: |
Institut für Automatisierungstechnik (IAT), Universität Bremen Rheinisch-Westfälisches Elektrizitätswerk (RWE) |
Time period: | 01.07.2018 - 30.04.2021 |
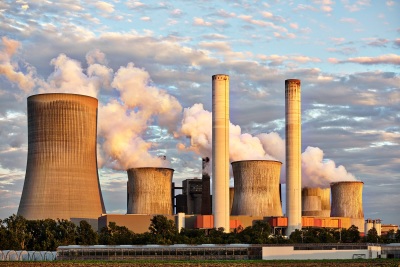
The project aims to improve the efficiency of a lignite-fired power plant of the energy company RWE. The functional principle of the power plant is as follows: First the lignite is burned so that the energy released can be used to heat water. The steam produced by the heat is then passed through one or more steam turbines via a pipe system. Once there, the steam expands in the turbine, causing it to rotate and drive a power generator.
The efficiency (and thus also the output) of such a power plant depends primarily on the steam mass flow and the steam temperature at the turbine. The strong and, due to the size of the power plant, also sluggish coupling of both variables makes their regulation difficult in practice, which is why the power plant cannot be operated optimally at the present time. A model predictive controller (MPC), the core of which will be TransWORHP, will overcome this shortcoming and maximize the efficiency of the plant.
A special feature of the project lies in the general conditions: For example, the MPC should not control the actuators of the plant, but rather run the existing control system with optimal setpoints. For the modeling of the power plant, this means that the control principle in the form of a subordinate control is part of the power plant model. The working group Optimization and Optimal Control supports the project around the topic "MPC with TransWORHP", but also develops an interface based on the "Functional Mockup Interface" to enable the communication of the modeling software Dymola with TransWORHP. Thematically relevant will be, among other things, the real-time requirements to the MPC. Here, under certain circumstances, a cascaded MPC control may be necessary, and the Optimization and Optimal Control working group will also support the implementation of this control.
Translated with www.DeepL.com/Translator (free version)